界面新闻记者 | 高菁
工作日早上9点,距离瑞典哥德堡市中心半小时车程的沃尔沃卡车Tuve工厂内十分安静,让人觉察不出这里是一个正在运作的重卡生产工厂。
乘坐观光卡车进入生产厂房内,与想象中严肃忙碌的工作场景不同,首先映入眼帘的是围在一起聊天、喝咖啡的工厂员工。这样的茶歇时光是Tuve工厂员工们的日常。
厂房中心设置了一片丛林地带,建有鱼池、种着棕榈树,工厂员工通常会选择在此处用餐。

与很多工厂不同,Tuve工厂厂房内的作业声较轻。据Tuve工厂负责人Peter Setterstig介绍,一方面,工厂会尽可能都使用电动化的设备工具,噪音本就不大;另外一方面,工厂在建造时便考虑到了噪音问题,通过特殊的建筑材料以及设计使之能够吸收部分噪音。
Tuve工厂在1982年投入使用,占地11.75万平方米,客户涉及全球100个国家。该工厂目前已实现碳中和运营。
碳中和运营,意味着企业在生产和运营过程中所产生的二氧化碳排放量与通过各种措施减少或吸收的二氧化碳量相等,从而达到平衡。
不同于4.0制造工厂的高度自动化,Tuve工厂的生产仍主要依靠人力,共有来自35个国家的2500名员工在此工作。
据Peter介绍,Tuve工厂共生产4种车型,FM、FMX、FH以及FH16。在此基础上,该工厂实行订单化生产。每一辆卡车,客户都有自己的特殊要求,对于配置需求均有所不同。
一般而言,一个卡车驾驶室包含超过900种零件,而Tuve工厂为驾驶室准备的零件高达3500种;驾驶室的颜色种类也达800种,仅白色就有36种,以供客户自行选择。
“在这样的生产背景下,批量化、自动化的生产模式难以满足需求。”Peter说。
为满足订单化生产需要,Tuve工厂卡车装配线采用鱼骨式结构,即以主装配线为核心,组装和预装配作业线作为分支紧靠主装配线。类似于搭积木的过程,卡车的子部件在组装和预装配作业线完成,作为半成品运输至主装配线,共同组装成一辆完整的卡车。
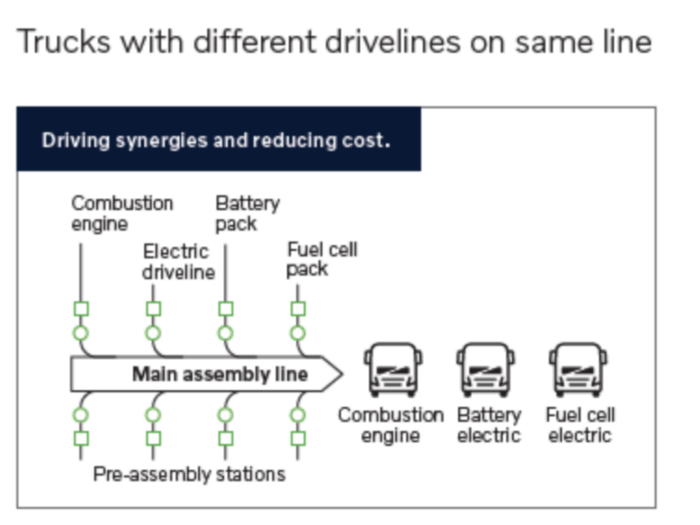
Peter称,工厂在主装配线上尽可能做到模块化、标准化,将变量分配至组装和预装配产线中,以此实现在同一条生产线上生产不同型号的卡车,满足不同订单的个性化需求。
在Tuve工厂,从车架部件到组装成成品卡车只需6个小时。去年全年,Tuve工厂共产出了2.7万台卡车成品,涵盖传统柴油驱动卡车、液化天然气卡车、电动卡车等,均出自同一条产线。
2022年三季度,Tuve工厂下线了第一批电动产品,包括FH、FM和FMX的电动版,自此成为了全球各品牌卡车生产商中第一个拥有系列电动产品生产的工厂。
Peter表示,“虽没有具体统计,但我们能够感受到,电动卡车的订单量在不断上升。”
目前,Tuve工厂电动卡车的电池电芯仍主要依赖外购,电池组装则通过沃尔沃位于比利时的电池组装工厂完成。
沃尔沃集团计划在2030年前建立大型电池生产工厂,电池将用于电动卡车、公共汽车、建筑设备等领域。该集团计划在2040年前实现全价值链净零排放目标,并提供100%安全、100%非化石燃料、100%产能提升的交通运输和基础设施解决方案。
除常规生产外,Tuve工厂还承担着沃尔沃卡车新产品的首次投放的任务。沃尔沃集团的最新卡车产品,如最新的FH电动卡车的首辆卡车,便是由Tuve工厂总装下线。

Tuve工厂内设有一个小型“试验田”,即试装线。用于与集团的技术部门和生产运营部门合作,进行新产品生产流程和所需技术的实验和验证。
在该试装线中,Tuve工厂会针对新产品进行新工具的实验验证和新生产流程的制定,并制定新的生产标准。这些标准和流程在试装线中完成后,再推广到其他工厂。
试装线使得工厂能够在新产品正式投产前,充分验证其生产流程和技术要求,确保新产品能够顺利进入大规模生产阶段。
针对全球正在崛起的造车新势力,Peter表示,“卡车市场当前竞争相当激烈,但Tuve工厂已经积累了40年的生产经验,我们会把过去的生产经验融入到新型电动卡车的生产过程当中。我们相信,这种经验使我们在市场上具有独特的竞争力。”
沃尔沃集团成立于1927年,为瑞典最大的工业企业集团,目前主要专注于卡车、客车、建筑设备、船舶和工业应用驱动系统的制造与服务。该集团在全球18个国家设有生产基地,并在190个市场从事经营活动,雇员约10万人。
2023年,沃尔沃集团共交付了约24.63万辆卡车,创下了历史新高,该部分业务实现了3730亿瑞典克朗(约合2587.83亿元人民币)的净销售额,占全集团净销售额的67.47%。
还没有评论,来说两句吧...